【中国事例】 FAW-TD:シミュレーション解析によるフェンダの寸法制御と調整
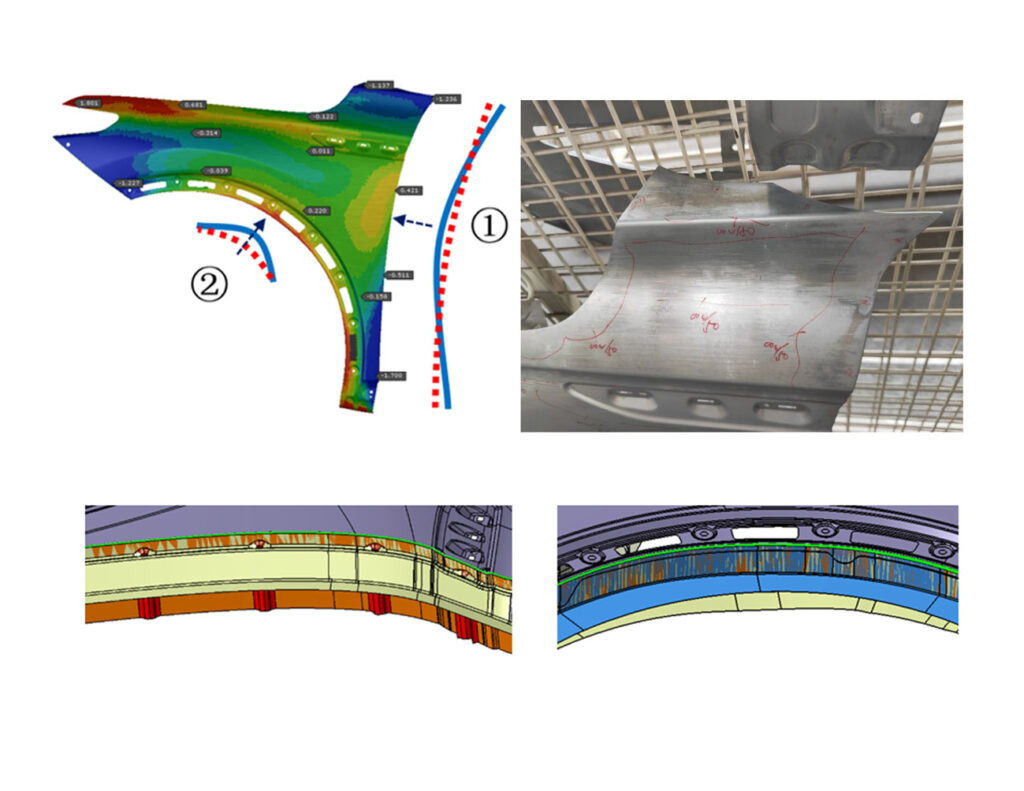
フェンダは、プレス成形工程が非常に複雑で、他のBiW(ホワイトボディ)部品と多くの合わせ面を共有しています。そのため、寸法精度と面精度ともに細心の注意を払う必要があります。本稿ではAutoForm解析を用いて高品質のフェンダを作成する方法について詳しく説明します。 基本部品および検査治具 図1. 部品設計&測定ツール設計 この部品のプレス成形には、ドロー、トリミング、フランジ、カムフランジ、リストライクの、合計5つの工程(5-OP)が計画されています。 図2. プレス成形工程の設計 AutoFormで成形性とロバスト性を検証した後、各工程のスプリングバック結果は次のとおりでした。 図3. 各工程のスプリングバック結果 OP40(カムのリストライク)では、Aピラー領域に顕著な寸法のばらつきが見られ、中央部が上方にクラウニングし、両端が下方に移動していることが明らかになりました。この不具合は見込み補正で修正したくなるのが当然ですが、しかし工程改善によってスプリングバックを最小限に抑えることが最善策です。過度な見込み補正による悪影響を回避できるためです。 図4. 初期スプリングバックの結果 Aピラー側およびホイールハウス部分の寸法精度が低いことが確認されたため、以下の方法で改善を図りました。 図5. 工程調整 • ゲイナー形状の追加: このステップにより、Aピラー側のフランジ加工時の材料の伸びの大部分が緩和され、 寸法偏差が緩和されます。 • フランジ加工タイミングの調整: ホイールハウス部分のフランジ加工タイミングを再設計します。 調整によって両領域のスプリングバックは大幅に緩和され、寸法は公差内に収まりました。さらにスプリングバック全体の分布も改善し、その後の見込み補正が容易になりました。 図6. 工程調整後のスプリングバック クランプシナリオの検討とクランプとスプリングバックの評価 クランプはパネルの寸法精度に大きく影響します。クランプが不十分だと、大抵の場合はスプリングバックのデータが非現実的になります。初期段階の検証を経て、以下のクランプ方案を用いることになりました。 部品を車両位置で測定し、最小クランプコンセプト(MCC)を適用しました。○は基準点システム(RPS)のクランプポイント、△はパイロットポイントを表します。2つのパイロットポイントがパネルを自重で固定し、XY方向の動きを制限し、6つのクランプがパネルをY方向に固定しています。 前述の工程調整と組み合わせることで、以下のスプリングバックの結果が得られました。 図7. MCC方案を用いたスプリングバックの結果 クランプとパイロットの荷重についても検証しました。クランプ荷重が過大になると、一般的にパネルがひずみ、スプリングバックのデータの信頼性が低下します。ここでは各クランプの法線荷重は 5N 未満であり、パイロット荷重はパネルの重量と等しく、シミュレーションの信頼性が確認できました。 見込み補正の方案 スプリングバックの結果から、ビーク部(No.2)、Aピラー(No.3)、ドッグレッグ部(No.1)に局所的な見込み補正を行うことにしました。OP10~OP40でこの見込み補正を行い、OP50では基準部品のサーフェスを使用しました(図8)。 図8. 見込み補正の方策 さらにAutoFormサーフェスへこみの結果や過去のプロジェクトで得た知見から、枠内で面精度に不具合が生じる可能性があると予想されました。この不具合に対処するため、その領域にローカルクラウニングの見込み補正を適用しました。 図9. サーフェスへこみ値が0.1 mmに到達 図10. ローカルクラウニングの見込み補正 これらの方案を適用した結果、クランプで拘束する方法の2つにおいて、スプリングバックの結果が改善されました。 図11. 2つの方法でクランプを拘束した場合のスプリングバック その結果、トライアウトパネルは測定ポイントの 91.3% が公差内に収まり、高品質なものになりました。シミュレーションと実際の結果は 0.5 mm 未満の誤差と、高い相関性を示しました。 図12. […]
【インド事例】 トライアウトの生産性向上:AutoForm を活用した金型たわみ解析
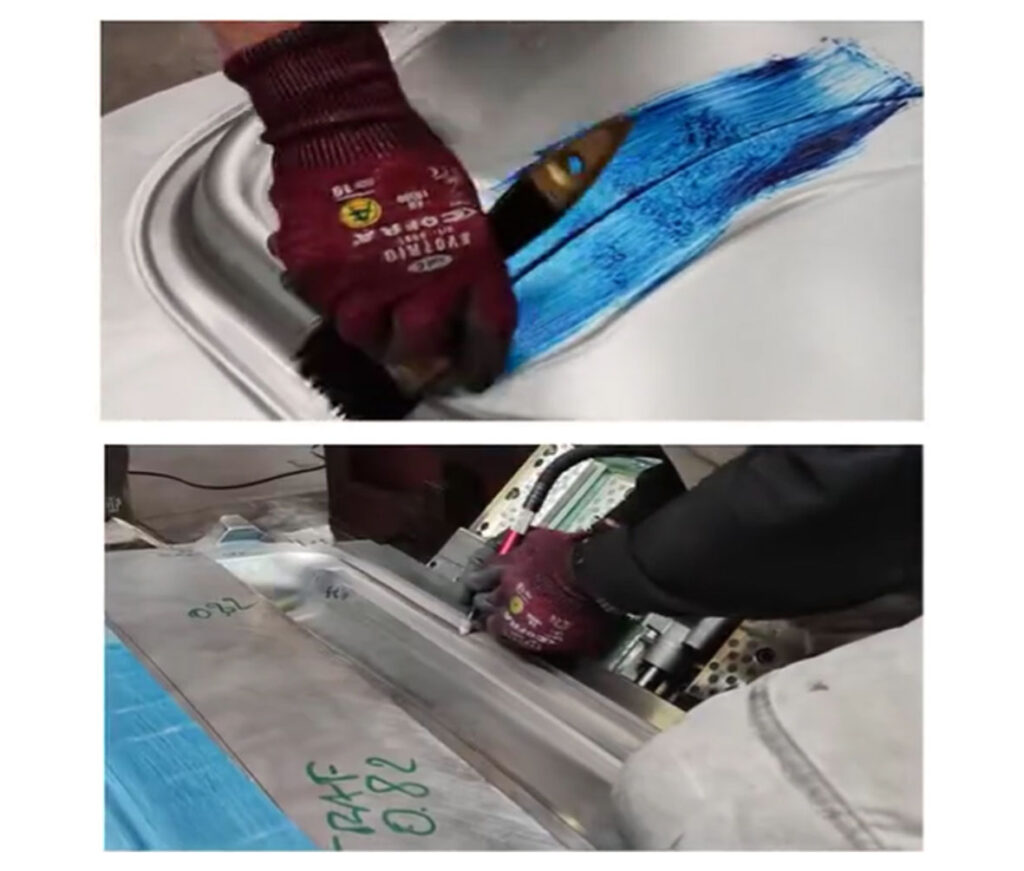
トライアウトではどの作業に最も高いスキルが求められるでしょうか? 答えは「ダイスポッティング」です。本稿では、さまざまな設備パラメータ、特に金型のたわみがダイスポッティングに与える影響、そして製造工程におけるデジタルエンジニアリングを活用した「フロントローディング」がトライアウト全体の時間をどのように短縮できるかを、オートフォーム・インディアのアプリケーションエンジニア、Sameer Chudnaik が解説します。 図1. トライアウトにおける手作業でのスポッティング 問題提起 トライアウト時間の約 35% から 40% は、初期のダイスポッティング作業に費やされます。特に主要部品の場合、品質改善を担う熟練のエンジニアには過大な負担がかかります。そのため品質改善業務が期日に間に合わない場合も稀ではありません。 負担過多の原因と工程改善を通じた緩和策 ダイスポッティングは、プレスの平行度、加工ばらつき、加工精度(加工中のカッターの摩耗など)といったさまざまな設備や工程のパラメータが影響を及ぼすため、難易度の高い工程です。本稿では「プレスと金型のたわみ」が与える影響に着目した検討を行います。 シートの変形中にはモーターから負荷がかかり、金型、ラム、ベッドが継続的にたわみます。通常、最大のプレス荷重は下死点で発生するため、経験則を用いて金型のたわみ値を計算することは困難です。金型のたわみは、以下のようなパラメータに依存します。 ダイにかかる引張力 ダイがプレス面積に占める割合 3D ダイフェースのバランス 金型の剛性 トライアウトでのスポッティングの時間が長引くことのないように、シミュレーションを用いてたわみを見込み補正する必要があります。 たわみの影響について 図 2. 左)負荷のない状態で金型が閉じると(BDC)上型と下型は直接接触します。 右)負荷がかかった状態で金型が閉じると(BDC)上型と下型はたわみます。 トライアウトでは、たわみによってシートの拘束条件が不均一になります。トライアウト担当エンジニアは、シートの両面に塗料を塗布し、ダイスポッティングを行います。これは手作業で行うため、熟練した技術が求められます。上型と下型のサーフェスを正確に一致させるスポッティング工程には、膨大な時間がかかる場合もあります。 手作業で行うスポッティングの工数を最小限に抑えるため、多くの企業では独自の手法を採用しています。 図 3. パンチとダイのたわみを補正する上で、上型のみにオーバークラウンを施しています。 下型のパンチはマスターとしてそのまま使用します(クラウンは適用しません) したがって、ダイのオーバークラウンは以下のとおり算出します。 ダイのオーバークラウン = ダイのたわみ + パンチのたわみ さらに調査を進める中で、プレス成形シミュレーションのファイル、金型設計の金型ソリッド、鋳造やプレスの弾性モデルなどの入力データを用いて、ダイのたわみを解析しました。ダイのデザインがない場合は、下図に示すように、AutoFormの基礎構造生成モデルを用いて金型ソリッドを生成することができます。 図 4. 上型のダイで 0.4 mm、下型のパンチで 0.5 mm の最大たわみ値が確認されました 経験則をもとにダイフェースのオーバークラウンを行う企業もありますが、金型の中心部にオーバークラウンを施しても、多くの場合、実際のたわみパターンは想定通りになりません。右図のように、トランクリッドのパネルでは、金型の最大たわみは中心からずれた位置に生じています。実際の最大たわみポイントは、形状や荷重分布によって異なります。 CAD ソフトウェア上にて、ダイの中心部を最大のたわみポイントとしてオーバークラウンを手作業で決定すると、トライアウト時に誤差が生じる可能性があります。実際の金型のたわみを正確に計算するには、手作業ではなくAutoForm などの高機能ソフトウェアを活用すべきです。金型のたわみをシミュレーションすることで、切削加工に適したオーバークラウンサーフェスを生成することができます。 最終的には、上型のダイと下型のパンチの両方のたわみデータをもとに上型をオーバークラウンすることに決定しました。下図はAutoForm を活用して生成したオーバークラウンのデータです。これは切削加工に使用できるものです。 図 5. […]
LINGYUN中国社の成功事例: サイドレールのアセンブリにおける溶接ひずみの予測と最適化
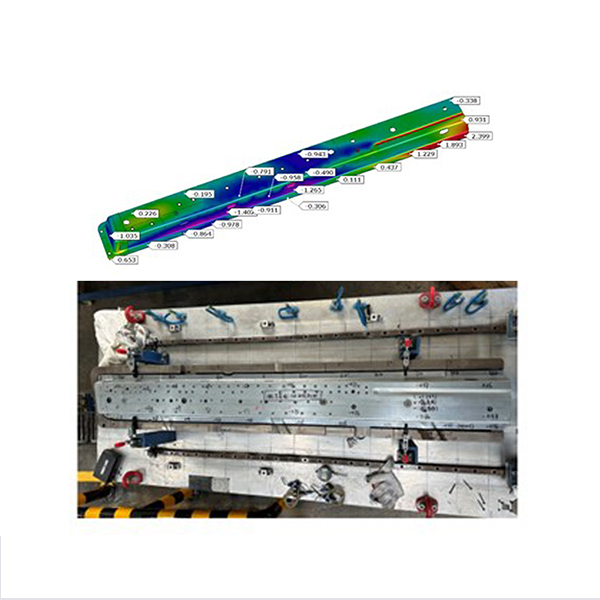
NIO中国社: BiWアセンブリのシミュレーションを活用して電着や焼付け塗装後の熱変形を排除
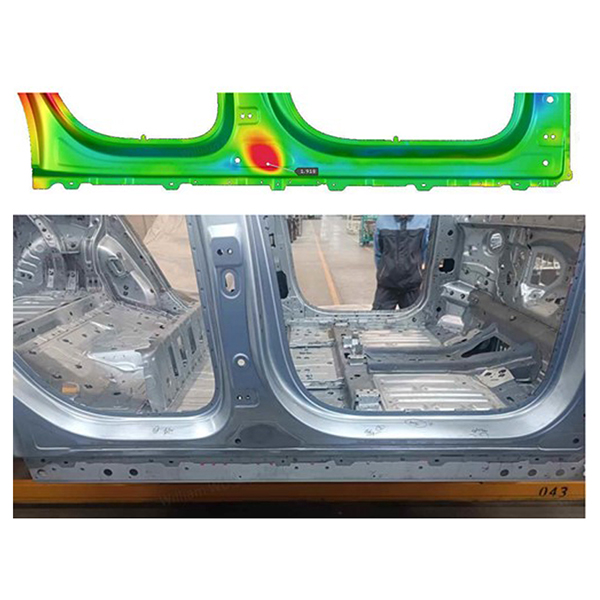
電着や焼付け塗装などの加熱・冷却処理を行うと、ホワイトボディ(BiW)のボディサイドアウター部分に座屈や波打ちといった恒久的な塑性変形が発生することがあります。このような不具合は車両の品質に大きな影響を与えます。一般的に、変形が生じる原因として以下の要因が考えられます。 加熱や冷却を通じて、サイドアウターパネルとインナーパネルの間に局部的な温度差が生じると、冷却後にアウタースキンパネルのサーフェスが不均一に変形し、不具合が発生することがあります。 ハイブリッドBiWでは、鋼材とアルミニウムの線膨張係数の違いが、加熱や冷却を繰り返すことで、鋼材のサイドアウターパネルのサーフェスに局所的な塑性ひずみが生じることがあります。 鋼材とアルミニウムのハイブリッドBiWでは両方の不具合が同時に生じる可能性があり、鋼材またはアルミニウム単一のBiWよりも不具合が頻発する傾向にあります。トライアウトや生産段階で対処する場合、複数部門による広範な検証対策が必要となるため、特に効率が悪くなります。 しかしCAEシミュレーションツールを活用して初期の製品開発段階で不具合を識別し、検証を行えば、これらの不具合を効率的に排除することができます。このように後工程を見越した対策を講じることで、量産時の不具合やその深刻度を大幅に軽減できます。 本稿ではAutoForm Assembly 熱硬化モジュールを活用した不具合の解析およびその回避策についてご紹介します。 AutoForm Assembly 熱硬化モジュールを活用した焼付け塗装のひずみ解析 シミュレーションでは、結果に大きな影響をおよぼす加工条件を、材料カードで正確に設定および定義する必要があります。 線膨張係数はAutoForm Assemblyによる焼付けのシミュレーションにおいて、最も大きな影響があるパラメータです。 熱伝導率は、材料の熱伝導のしにくさを示します。 対流熱伝達率は、流体と固体のサーフェス間の熱伝達能力を表します。これは焼付けのシミュレーションにおいて、シミュレーション対象物と周囲環境に対して定義します。 前処理 解析の前処理、つまりシミュレーション設定には複数の工程が必要となります。 まず材料の板厚方向、材料の板厚、材料モデル、熱力学パラメータなどを設定します。本稿の対象であるインポート済みのサブアセンブリを図1に示します。 工程計画ステージでは、工程数や各工程で組み立てる部品/サブアセンブリを決定し、図2に示すとおりアセンブリシーケンスツリーを作成します。 図1:AutoForm Assemblyにインポートしたサブアセンブリ 図2:アセンブリシーケンスツリー 組付け治具への設置と固定を行う際には、各部品/サブアセンブリの接合時に安定性が担保されるように、工程ごとに設置順序(図3)、設置方向、位置決め、クランプの方策を検討する必要があります。 次に接合と接着です。本件ではスポット溶接、接着(図4)、FDSを使用しますが、FDSはまだソフトウェアに実装されていないため、代替モデルとしてリベットを使用します。 図3:設置順序 図4:シミュレーションで使用する接着 シミュレーションでは最後に熱力学パラメータ(線膨張係数、熱伝導率、対流熱伝達率)を部品や材料ごとに定義します。熱伝達率は、鋼材で45mW/mmk、鋳造アルミニウムで220mW/mmk、熱間プレス成形の鋼材では23.3mW/mmkに設定します。 また本体と周囲環境間の対流熱伝達率は0.02mW/(mm^2・K)に設定します。 さらに焼付け時の加熱時間と温度保持時間は、実際の加工条件に合わせて設定します。 シミュレーション結果の考察 サイドパネルの変形をシミュレーションする場合、その結果の品質は、主に変形の程度とバーチャルオイルストーンの性能によって決まります(図5)。 図5:サイドアウターパネルの変形 図6:ボディサイドのアセンブリにおけるアルミニウム押出ビーム材 サイドアウターパネルの下側部分に1.9mmの著しい膨張が見られますが、これはアルミニウム押出ビーム材の線膨張係数が他の鋼材パネルよりも高いことに起因します(図6)。 この変形は加熱や冷却から生じたものです。もし塑性変形の値が滑らかな勾配をもって変化し、局所的に急激なばらつきを持たなければ、実際の車両では面ひずみはほとんど検出されません。そのため、この塑性変形の量を構造的な剛性の指標として、構造設計の初期段階における剛性の最適化のために使用することができます。 図7はバーチャルオイルストーンの結果を示しています。Bピラー下部の両端で最大0.17mmという急激な値が確認されました。これらの結果から、この領域で波打ちが生じていると結論づけることができます。 図7:X方向のバーチャルストーニングの結果 図7の結果は加工条件下でのへこみや波打ちといった面ひずみの可能性を示唆しています。したがって、この結果を焼付けによる変形の影響を受けた面精度の最終評価の指標として使用します。 シミュレーション結果の検証 図8および図9では焼付けの前後における実際のアウターパネルを比較し、変形傾向とシミュレーション結果との相関性を紐解きます。 図8:焼付け前のBiW 図9:焼付け後の状態 Bピラー下端付近では膨張による変形が検出され、図5が示す傾向と一致します. 図10:焼付け後のBピラー部分のスキャン結果 図10にスキャン結果が示されているとおり、焼付け後にBピラー領域には正規寸法からの偏差が生じます。図5と比較すると、膨張による変形は傾向と分布の両方でシミュレーション結果と高い相関性があり、焼付けによる変形のアセンブリシミュレーションは非常に高精度であることがわかります。 まとめ サイドパネルの焼付けによる変形は、自動車業界における長年の課題です。この不具合に対処するためには、既存の解析ツールでは限界があり、構造的な剛性の設計がどのように影響するかを効果的に評価できませんでした。従来は、余分な補強材を追加するなどの対応がとられてきましたが、これにより効率が低下し、コストも増加していました。しかし熱硬化のシミュレーション技術が採用されたことで、サイドパネルの焼付けによる変形を正確に評価できるようになり、構造設計を効果的に改善することが可能になりました。この手法により、車両製造時の不具合に関連するリスクが大幅に低減され、余分な補強材のコストも削減可能となりました。 さらにこのタイプの解析は、複数の材料タイプを使用したドアなどの他のサブアセンブリにも適用できるため、潜在的なメリットはさらに広がります。 NIO社のコメント デジタルシミュレーション担当部署のリーダーであるトゥ氏は、このような不具合対応を広範に適用できる可能性について示唆しています。「ハイブリッドBiWを扱う多くの企業が焼付けによる変形の不具合に悩まされています。AutoForm Assemblyを活用して初期段階から対策を講じることで、トライアウトや量産における潜在的な損失を削減することができます」 著者について シャオウェン・トゥはデジタルシミュレーション技術部を率いるほか、NIO社フォーサイト製造技術部門に属するプレス成形工程に精通した技術者でもあり、自動車業界で22年の経験と数値シミュレーション技術に精通しています。 ペンペン・リュウ・シャオキアン・パンは、NIO社フォーサイト製造プロセスイノベーションセンター部門の主要メンバーです。 […]
Starq Y-Tec社ではホワイトボディのアセンブリ工程を正確に予測し、トライアウト回数を大幅削
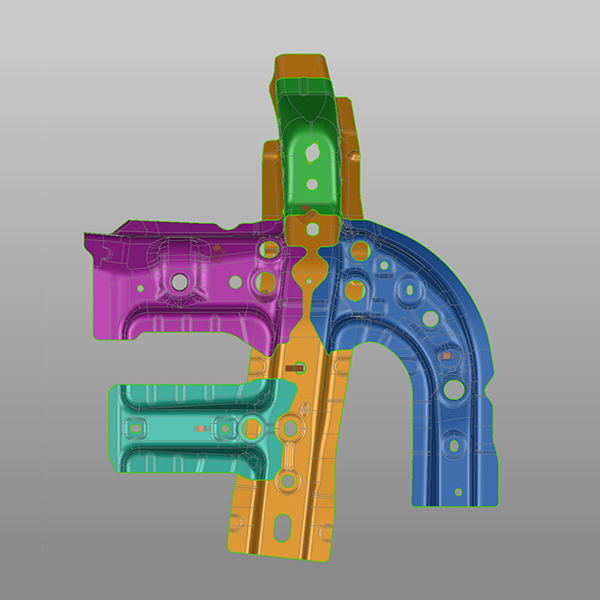
概要 先んじて実施された イタリアFontanaグループとの共同プロジェクトにおいて、プレス成形工程およびアセンブリ工程の解析ソフトウェアであるAutoFormが非常に高精度であることが確認されました。その後、マツダやBYDのTire1サプライヤであり、BiWコンポーネントのプレス成形およびアセンブリを請け負う中国Starq Y-Tec社の現場にて、新たな検証プロジェクトが実施されました。 本稿ではStarq Y-Tec社がAutoForm Assemblyを活用し、最終製品に至るまでの工数を大幅削減した事例について紹介します。 課題 Starq Y-Tec社は大手メーカーを顧客に有する単品部品のプレス成形およびアセンブリのサプライヤです。当時はアセンブリ工程をシミュレーションできるデジタル・ツールは使用しておらず、すべてアナログで組立作業を行っていました。そのためアセンブリ工程で生じうる不具合を事前に特定できる手段は何もありませんでした。 ある顧客のフロント・サイド・メンバーを製作する中で、アナログな作業には多くの無駄な試行錯誤が伴うという気づきがありました。 単品のプレス部品は仕様と完全一致しているとは言い難くも、基準形状とは大差ないものでした。プレス成形部門での作業時にはスプリングバックの問題に対応しましたが、部品が仕様の範囲内に収まると、アセンブリ部門による組立作業に移行しました。 しかしプレス部品を組み立てると、部品が設計通りにはまらないことが判明したのです。そこでエンジニアリング部門まで部品を戻し、デザインの見直しが行われました。部品設計の修正からプレス成形やトライアウトまで含めると、この見直し作業には約2~3週間を要しました。 それでもトライアウトでは十分な結果を得ることができませんでした。そして最終的に仕様が満たされるまで、この一連の作業を何度も繰り返すことになったのです。ここでご留意いただきたいのは、単品のプレス部品は初期の設計から公差に収まっていたという事実です。 Starq Y-Tec社副社長Li Qi氏は次のように述べています。「デジタル・ツールを活用してアセンブリの不具合を事前に予測しなければ、最終段階まで不具合対応に追われることに気づきました。初期段階にて多大な労力をかけて単品部品を公差に収めたにも関わらず、後期段階ではその部品を組み付けることができず、単品部品の設計やトライアウトからやり直しました。これには莫大なコストと時間がかかります」 プレス成形やホワイトボディのアセンブリにおいて、このような事例は頻繁に生じています。OEMでも部品に修正を加えて最終アセンブリに対応したといった事例も多くあります。またアセンブリ部門による部品の組み付けが上手くゆかないと、エンジニアリングやトライアウトの部門に立ち戻り部品設計を見直す必要があるため、アセンブリ部門で生じた不具合の対応に追われることに不満を感じる場合もあるようです。 不具合への対応策 アセンブリ部門では不具合を検出すると、以下のタスクを繰り返しながら工程を修正してゆくことで、アセンブリの改善を図りました。 クランプの位置や順序の変更 溶接の位置や順序の変更 単品部品のさまざまな修正 不具合が解消されるまで、このトライ&エラーのループを4回以上も繰り返す必要がありました。1回あたり2~3週間を要するため、この方法には膨大な時間がかかるだけでなく、非常に複雑で非効率であることも明らかです。 開発期間の長期化、コスト上昇や生産遅延、最終製品や金型の品質低下といった問題が生じるだけでなく、生産が遅延しないよう従業員が残業を強いられるなど、時間やコストに過剰な負担が生じることは言うまでもありません。 このように計画性がない生産活動の中で軽視されがちなのが、実際の作業にあたる担当者の心の健康です。明確な目的が示されずに仕事量のみが急増することで疲労や不満が増大し、士気や自信も低下します。エンジニアリング、アセンブリ、トライアウトの部門間で業務に対する責任の擦り合いが生じ対立が深まると、さらに悪影響が広がります。 このような負の関係性は、残念ながら多くの生産現場で見られるようです。しかしながらデジタル・シミュレーションを活用すれば、アセンブリを良好に進めるためにどのような修正を行うべきかが明確になり、このような部門間の対立もすぐに解消されるでしょう。 AutoFormソリューション Starq Y-Tec社の上層部は、アセンブリの不具合を事前に予測できれば、このような問題を回避できると判断しました。常に納期短縮を目標に掲げ、不具合の対応に数週間はおろか数日の猶予すら嫌がる大手メーカーの顧客満足度を高めるには、より迅速で信頼できるソリューションが必要でした。 そしてStarq Y-Tec社ではAutoFormソフトウェアによるアセンブリのシミュレーションについて、検証プロジェクトを立ち上げました。このプロジェクトでは2段階の検証を行いました。 アセンブリ工程で生じうる不具合や課題をAutoFormソフトウェア上で正確に再現できるかを検 証。またシミュレーションの実行前には実部品を測定。使用した部品は5個のコンポーネントで構成 されたフロント・サイド・メンバー。材料はSPCM980YL-55/55、板厚は1.8mm。 AutoFormシミュレーション結果と実部品の実測値を比較し、シミュレーション精度を検証。 結果 AutoFormシミュレーション結果は、実際のアセンブリ部品の実測値に非常に近いことが判明しました。 比較を行うため、合計104カ所で測定を行いました。差異が0.5 mm未満であったのは80カ所、そのうち56カ所は0.3 mm未満でした。 残りの24カ所は差異が0.5mm以上でしたが、1mm以上の差があったのはわずか6カ所です。 アセンブリのシミュレーションでは、実際のアセンブリ部品と非常に近い結果が得られました。50%以上が0.3mm以内、74%がアセンブリ部品の0.5mm以内でした。 シミュレーションを使えば、アセンブリ工程における不具合を高い精度で予測することができます。しかもすべて比較的短時間で行えます。 ソフトウェアをより広範に活用すれば、工程のバーチャル・モデルを作成し、実際の製造現場で実施しているトライアウトの回数を大幅に削減することすら可能になります。 唯一無二のAutoFormソリューション AutoFormには、競合他社にはない以下3点の優位性があります。 あらゆるアセンブリ工程のモデル作成工程を詳細に表現するために必要な幅広い金型と設定を備えています。そのため、さまざまなアセンブリ工程のモデルを作成することができます。 […]