Success Case : 北京ベンツ汽車有限公司(中国)
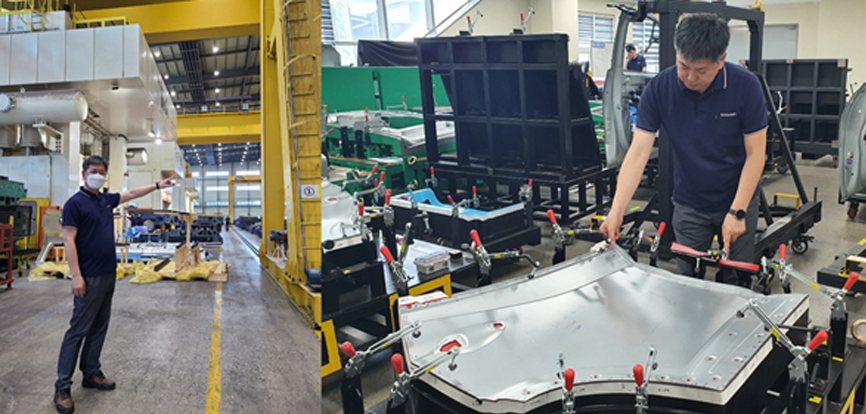
北京ベンツ汽車: トランクリッド・インナーパネルの成形最適化 トランクリッド・インナーパネルの製造工程は、温度や材料特性の変動に非常に敏感であるため、生産中にしわやわれが多発します。北京ベンツ汽車ではこの不具合を解消するために、CAE解析を用いて生産能力を分析的に検討し、工程パラメータ、金型形状、設備設定、材料特性の最適化を行いました。 トランクリッド・インナーは、標準的なボディ・インナーのパネルです。この部品の表面形状は複雑で、全体寸法が大きく、突起や溝が多いため、プレス成形時にわれやしわが生じやすくなっています。この車種のトランクリッド・インナーパネルを生産する際には、図1に示すように、しわとわれが交互に発生することが多くあります。 クッション圧や潤滑などの工程パラメータは、バッチごとに調整が必要です。これは生産効率に影響を及ぼすだけでなく、補修や廃棄も多く生じるため、このような不具合は特に解消が急がれます。 図1. 部品の不具合(しわ、スリップライン、われ) 基本情報 図2. ドロー形状 工程計画 以下の通り計画された5つの工程で部品のプレス成形を行います。 OP10 ドロー; OP20 トリム/CAMトリム/ピアス; OP30 トリム/CAMピアス/ピアス; OP40 リストライク; OP50 CAMピアス/ピアス。OP10のドロー形状を図2に示します。 シートの形状および特性 図3に示すように、ブランクは円弧のような形状をしています。シートの情報および特性は、それぞれ表1および表2をご確認ください。 図 3. シート形状 表1. シート情報 表2. シート特性 不具合解析 低い安全マージン この部品のCAE解析結果から、板減25.9%(図4)、マックス・フェイラーは0.9(図5)であることが判明しました。その結果、われの危険性が高く、設計段階での安全マージンが不十分であることがわかりました。 図4. 板減 図 5. マックス・フェイラー 生産検証では、図6に示すように、材料が滑ってしわになるところから部品われに至るまで、材料流入の幅が12mmあることが確認されました。 図 6. スリップラインの金型マージンは約12mm 温度に敏感な金型 生産初期は金型温度が低いため、スリップラインが大きくなります。生産中盤から後半にかけては、シート材と金型の摩擦によって金型の温度は上昇し続けます。熱膨張と冷収縮の原理によって上型とブランクホルダのギャップが小さくなると、材料の流入の抵抗が大きくなり、部品がわれやすくなります。生産開始から約950個生産するまでに、図7に示すように、スリップラインの位置が約9mm変化しています。 図7. 生産開始から950個の生産時までスリップラインが9㎜変化 材料特性の変動に敏感な金型 この金型は材料特性の変動に敏感です。図8に示すとおり、生産工程で材料コイルを交換すると、スリップラインの位置も6mm程度変化します。 […]
Success Case : SEPYON TOPMETAL社(韓国)
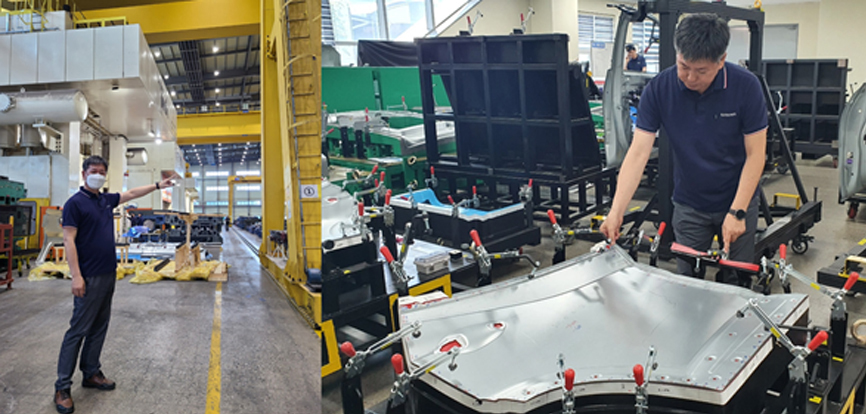
正確度指標: シミュレーションとトライアウトの設定条件を一致させ、初回トライアウトで高評価を獲得 韓国のSeoyon-TopMetal社は、HKMC、Daimler、BMW、VW、GMなど国内外の自動車メーカーを顧客に持つ金型メーカーです。1987年に設立された同社には、金型製造に精通した人材と国内最高峰の設備が揃っています。サプライヤとして公式認定されており、常時フル稼働しています。またカーボディ・アウターおよびインナー、さらにはアルミなど多岐にわたる金型製作の実績とノウハウを元にプレス金型製作の技術開発にも力を注いでいます。 図1: CAEチームリーダーによるトライアウトの品質確認 Seoyon-TopMetal社ではAutoFormを長年活用し、信頼性の高い検討を数多く行ってきました。特に2019年には、トライアウトに関する多くの実績からCAE担当部署の存在感が大きく高まりました。実際のトライアウトに適用するために必要な設定条件の指標となる「正確度指標」をシミュレーションに適用し、それらの確認および検証を継続したことで、現在では精度が30%以上向上し、トライアウトの工数が大幅に軽減されたのです。 さらに、Seoyon-TopMetal社が製造したアルミパネルのフロントドア・アウターの初期品質は85%以上、スチールパネルのリアドア・アウターに至っては95%以上という高評価を獲得しています。本稿ではこうした改善に至った経緯についてご紹介します。 図2: トライアウトの設定条件と同様に部分的なベアリングを適用 AutoFormのシミュレーション・モデルと同じ結果をトライアウトで得るには、両者で流入を合わせることが最も基本となります。バインダーのベアリングを調整することで、初回トライアウトでビードを修正する時間を最小限に抑え、流入の傾向をシミュレーション結果と同様にすることができます。AutoFormの「部分的なベアリング」機能を活用すれば、非常に簡単に、関連領域のみを指定して一致する設定条件に合わせることができます。ビードの拘束力はバインダーのベアリングに応じて差が出ます。流入量が多い案件では特に顕著となり、また傾向もさまざまです。上図では部分的なベアリングを定義して、ビード外周のハードスポットを除去しています。 図3: トライアウトの設定条件と同様にパッドにリリーフを適用 そして、最も工数がかかる部分が、成形時のパネル変形を予測し、事前に問題を改善する業務です。それには2通りの設定条件を適用できますが、比較的簡単に設定できる条件がパッドのリリーフとなります。成形性に対する影響が少ないため、エンジニアリングの初期段階では適用しませんが、スプリングバック解析を正しく実行する上では不可欠なものです。各工程でシートのR部分に負荷がかかりすぎないように、R形状と工程中に閉じる必要がない領域にリリーフを適用します。「凹半径の削除」機能を適用するだけで、R形状を金型から削除できます。この操作を行うと、シミュレーションでパッドに荷重がかかりすぎることはありません。つまりR形状をこのように設定すれば、パッドが閉じる間にさらに成形が進行することがなくなり、パネルの変形を極力抑えることができるのです。 図4: ドローシェル見込み補正による位置決め状態の改善 また、2次成形時のシートの位置決めを最適化する場合にも、多くの工数がかかります。パネルの変形を回避するには、工程間の位置決めも配慮が必要となります。アルミのようにスプリングバックの影響を受けやすいものでは、次工程の金型を見込み補正する場合、前工程で成形したパネル形状の結果がベースとなるようにしなければなりません。これを確実に行うには、AutoFormのドローシェル見込み補正を活用できます。そしてスプリングバック解析とAutoForm-Sigmaでロバスト性解析を実行し、見込み補正について判断を行います。 図5: ドア・アウターの見込み補正戦略 信頼できる結果を得た後、上図のように見込み補正を行いました。最後のスプリングバックを基本に全工程の金型に見込み補正を行い、見込み補正後の位置決め状態を分析し、影響を受ける工程に対してはドローシェル見込み補正を行いました。 図6: 見込み補正後の最終検証におけるスプリングバックの結果 トライ&エラーを重ねながらも工程間で生じる変形を最小限に抑制すると、図6のように良好な結果が得られました。また初回トライアウトでも同様の結果を得ることができました。 アルミパネルの案件を開始した当初には、多くの問題が山積していました。AutoFormのシミュレーション結果と実際の現場で得られる結果には差異があり、問題を解決するためにトライアウトで多くの時間を費やしていました。しかし本稿で紹介したとおり、エンジニアリングの段階にてパネルの変形をシミュレーションで特定し、事前に対策を講じることで、実際のトライアウトにて良好な結果を得ることができるようになったのです。 要旨 プレス成形時に生じるパネルの不本意な変形を事前に改善することで、AutoFormとトライアウトの結果が一致するようになり、信頼性と精度が高まりました。その結果、スチールパネルのリアドア・アウターとアルミパネルのフロントドア・アウターについては、初回トライアウトにて、それぞれ85%以上、95%以上の高評価を達成しました。エンジニアリングの段階ではより多くの工数が必要となりますが、トライアウトの修正に必要な作業量は50%以上削減されました。
Case Study :「熱間プレス」と「冷間プレス」の比較に見るCO2排出量削減
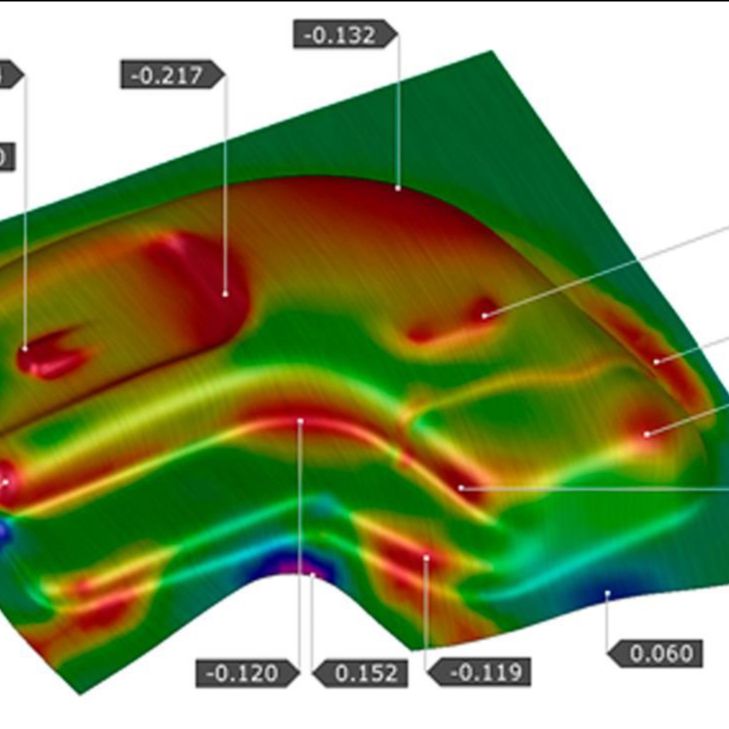
「熱間プレス」と「冷間プレス」の比較に見るCO2排出量削減 CO2排出量の削減は、近年、世界的に最も注目されているテーマの一つです。製造業においてこの動向を後押しする要因は、国際法への準拠、炭素税の高騰、社会的規範、消費者の環境意識変化などが挙げられます。自動車産業におけるCO2排出量削減の取り組みとして、冷間および熱間プレス成形技術を深く考察することで、バリューチェーン全体から生じる排出を把握することができます。冷間プレスと熱間プレスに優劣はあるのか、また将来的に優先的に採用すべきプレス成形技術はどちらであるか、併せて考察します。 CO2排出量の算出方法 冷間と熱間のプレス成形技術を詳細に比較分析する前に、まずCO2排出量の算出方法について説明します。適正な比較検討を行うには、ガイドラインとなる標準が必要となります。そこで温室効果ガスの国際基準として広く採用されているのが、世界資源研究所(WRI)と持続可能な開発のための世界経済人会議(WBCSD)が政府、NGO、企業の協力を得て策定したGHG(温室効果ガス)プロトコルです[1]。従って本稿では、GHGプロトコルの基準、特に「スコープ1~3」のコンセプトをもとにGHG排出に着目した冷間プレスと熱間プレスの比較を行います。 「スコープ1~3」とは バリューチェーンにおけるCO2排出はすべてスコープ1、2、3 に分類できます。スコープ1は調査対象の会社の企業活動で発生するすべての直接的な排出をまとめたもので、たとえば、炉でのガス燃焼などが該当します。電力など、購入したエネルギーの消費については間接的な排出として、スコープ2に分類されます。スコープ3はスコープ2に該当しない間接的な排出で、これはバリューチェーンの上流と下流の活動に分類されます。上流側の例としては購入する鉄鋼材料に関連する排出、下流側の例としては自動車を運転する際の燃料消費などが相当します。 スコープ 1~3とプレス部品の関係性 図2が示すとおり、CO2はさまざまな形態で排出されています。しかし冷間と熱間のプレス成形技術の比較においては、すべてが関連しているわけではないため、いくつかの排出形態を選び出し、より詳細な分析を行いました。 スコープ1の直接的な排出は、熱間プレス成形のみが該当します。シートの焼きなましにガス燃焼炉を使用する場合、プレス工場で燃焼するガスからGHG排出が生じています。しかし電気炉あるいは電気とガス加熱を併用したハイブリッド炉を使用すれば、排出量を削減することができます。冷間プレス成形から直接的なGHG排出は生じないため、CO2排出量削減の観点においては、スコープ1では熱間プレス成形が劣位にあります。 スコープ2の間接的な排出についても、冷間プレスが優勢だと思われます。なぜならば熱間プレスでは、大量の電力を集中的に消費するためです。油圧プレスのみならず、ブランクカッターや冷却器、エネルギーを大量消費する最終切断用レーザーなどの設備にもエネルギーを供給しなければなりません。また部品のサイクルタイムも比較的長くなるため、必然的に部品毎の排出量も多くなります[3]。 スコープ1と2の分析は比較的容易ですが、スコープ3になると分析はより複雑になります。熱間プレスの唯一決定的な弱点は、ガス燃焼炉用のガスを購入しなければならないことです。燃焼用ガスを使用する場合、ガスの抽出と輸送から非常に多くのGHG排出が生じます (ドイツでは12.5%)[4]。しかし一方で、購入する鉄鋼材料の分析はより複雑になります。たとえば22MnB5とDP1000を比較する場合、両者には合金にわずかな違いがあるだけで、工程ルートにも大差はないため、材料等級自体がGHG排出に大きく影響することはありません。しかしここで着目すべき点は鉄鋼材料の量です。熱間プレスの利点は、複雑なアセンブリを簡略化でき、また部品を軽量化できることにありますが、これはGHG排出の観点からも非常に有利に働きます。つまり、熱間プレスによって各部品をどれだけ軽量化でき、上流のGHG排出を削減できるかが、スコープ3における比較のポイントにもなるのです[9]。スコープ3の下流側にて熱間プレスが優位にあることは一目瞭然です。最終製品を1グラム軽量化するごとに燃料消費量が減り、アセンブリを簡略化するごとに後続の接合工程の回数が少なくなります。 特記事項 排出の性質を理解することで、プレス成形工程を冷間と熱間のそれぞれで行った場合のCO2排出量を比較することが可能になります。まずは熱間プレスがもたらすメリットとその程度を把握することから始めます。熱間プレスで部品を製造すると、重量はどれくらい削減できるのか、また、冷間プレスで製造した複数のプレス部品を組み付ける代わりに、熱間プレスによる単品部品で代替することはできるのか、といった可能性を検討します。これらはすべて鉄鋼材料の量も関係してくるため、スコープ3の排出量に直接的な影響があります。 熱間プレスのみで生じるスコープ1の排出も、必ずしも発生するとは限りません。たとえば炉に再生可能エネルギーを用いるなど、CO2ニュートラルなエネルギーを活用できる場合もありうるからです。ガスをエネルギーとして使用する場合でも、スコープ1~3の分析[5]から外された、別枠として考慮されるバイオガスに切り替えることができます。しかしバイオガスを使用する際には、留意すべき点がいくつかあります。まずバイオガスの生産に使用する土地は、食料生産に使用している土地から転用しなければいけません。またバイオガスの生産時には、有害な物質が排出される可能性があることにも注意が必要です[6]。複雑な現状を評価することの難しさに加え、CO2削減に関する多くの研究が進んでいることも重なり、状況はより複雑さが増しています。 最新の研究動向と着目点 鉄鋼業を環境に優しい生産へ転換することは重要課題であり、プレス工場のスコープ3の排出にも大きな影響を及ぼします。そのため鉄鋼メーカーではさまざまな手段で脱炭素化を進めています。中でも化石燃料である石炭を使った溶鉱炉での還元の代わりに、環境に優しい水素を使った直接還元に置き換えることができれば、これがゲームチェンジャーとなり大きな変革が進むと予測されています[7]。これが実現すれば、環境に優しい電力エネルギーを利用し、電気アーク炉で銑鉄を生産することが可能となります。 また冷間プレスの技術開発としては、熱間プレスに対抗して、高強度鋼から複雑な形状を製造する取り組みも進んでいます。たとえば、金型を分割し複雑な機構を与えることで、それぞれ異なる速度で移動する金型コンポーネントを個別にコントロールし、従来の冷間プレスでは対応できなかった部品形状が実現できるようになります[3]。 一方、熱間プレスについては、環境面を改善する取り組みが進んでいます。その一例として、ホンダ社ではエネルギーを多く消費するレーザー切断に代わり、成形時に部品を直接トリミングする手法を推進しています[資料8]。 CO2削減の取り組みにおけるシミュレーションの活用 CO2の排出に関わるパラメータを把握し、定量化する上で、プレス成形シミュレーションが重要な役割を果たします。熱間プレスあるいは冷間プレスの最終決定を行う前にシミュレーションを活用すれば、ブランクサイズ、材料板厚、部品重量、BiWアセンブリ、サイクルタイムなど、すべて徹底的に調べ上げることができます。 部品製造に熱間プレスと冷間プレスのどちらを用いるかを検討する際には、プレス成形シミュレーションのフィージビリティ評価をその根拠として活用することができます。技術的な観点から熱間プレスを用いることが決まれば、スコープ1と2に相当するCO2排出は明らかに多くなります。しかしその一方で、部品を軽量化することで、スコープ3のCO2排出を削減することができます。 すでに工程が決定している場合でも、ブランクサイズの最適化/最小化によって、スコープ3の排出は大幅に削減されます。使用する材料を1グラム削るごとに、CO2削減に対する大きな貢献となるのです[9]。最小ブランクの検討は、初期の製品開発から部品生産までプレス成形プロセスチェーン全体を通じて、シミュレーションを活用した取り組みが行われています。 明確な答えはありません CO2排出量が多いのは熱間プレスと冷間プレスのどちらであるかを厳密に定義することはほぼ不可能です。GHG基準を遵守するには、多くの影響因子を個別に検討しなければいけません。熱間プレスはガスの燃焼が不可避なためCO2排出が多いと思われがちですが、しかし部品の軽量化やアセンブリの簡易化が進むことで部品単位でのCO2が削減されるため、スコープ3のCO2排出を抑制できます。また多くの企業がさまざまな角度から研究開発戦略に取り組んでいるため、今後数年のうちに明確な答えが導かれるような状況でもありません。そのためシミュレーションを活用して予想されるCO2排出量を把握および定量化し、熱間プレスと冷間プレスのどちらを選択するかを検討するための判断材料とすべきなのです。 参考文献[1] Green House Gas Protocol, Access Date: April 22, 2022[2] Foundation myclimate: What are Science-Based Targets (SBT)? Access Date: […]